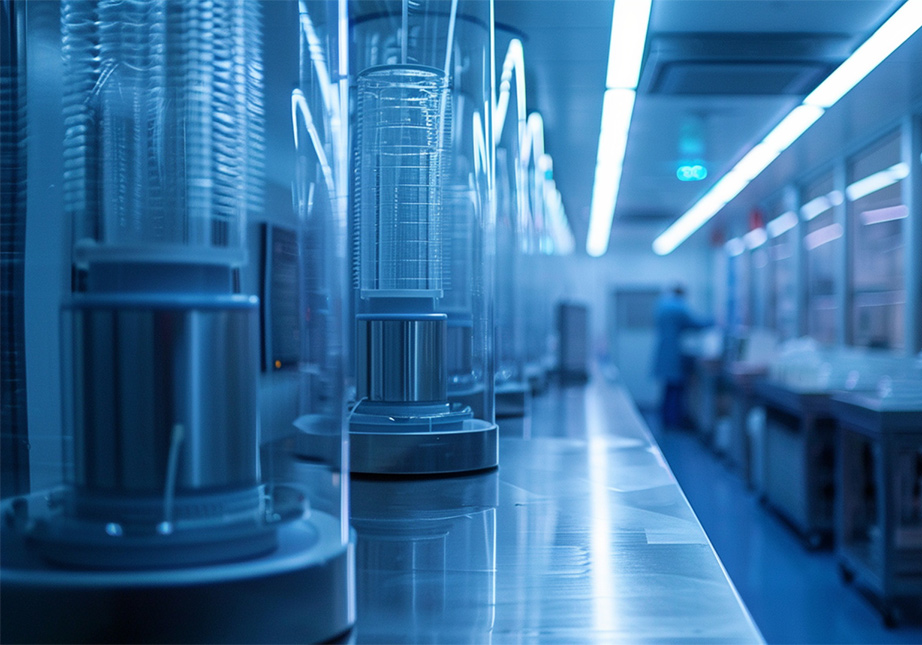
Jun 05, 2024
Cleanrooms for Biotechnology
Understanding Cleanrooms in Biotechnology
Cleanrooms are specialized environments with controlled levels of pollutants such as dust, airborne microbes, aerosol particles, and chemical vapors. In biotechnology, they are essential for maintaining the sterility and integrity of the research and production process. Cleanrooms are defined by their cleanliness classification, which is determined by the number of particles per cubic meter at a specified particle size.
The Role of Cleanrooms in Biotech
In biotech research and production, cleanrooms prevent contamination that could otherwise lead to inaccurate test results or compromised product quality. They are integral to the development and manufacturing of pharmaceuticals, vaccines, and other medical products where sterility is paramount.
Ensuring Process Integrity
To ensure the integrity of biotechnological processes, cleanrooms employ advanced air filtration systems, such as HEPA and ULPA filters, to remove contaminants from the air. The design and materials of cleanrooms are also tailored to prevent the accumulation and spread of pollutants.
The Necessity of Controlled Environments
A controlled environment is crucial for biotech advancements because it allows for the precise manipulation of biological samples and the production of consistent, reliable products. Without the stringent control of environmental variables provided by cleanrooms, the risk of contamination could significantly hinder progress in biotech research and innovation.
By maintaining a controlled environment, we at G-Con ensure that your biotechnological processes are carried out in a space designed to support the highest standards of cleanliness and compliance. Our commitment to quality and innovation in cleanroom design is reflected in our tailored solutions that meet the specific needs of the biotech industry.
Standards and Classifications for Biotech Cleanrooms
Understanding the standards and classifications for biotech cleanrooms is essential for ensuring the integrity of your research and production processes. At G-Con, we recognize the importance of adhering to these guidelines to maintain a controlled environment that is crucial for biotech advancements.
ISO Classifications Relevant to Biotech Cleanrooms
ISO classifications define the level of cleanliness in cleanrooms by the number of particles allowed per cubic meter at a specified particle size. For biotech applications, ISO Class 5, equivalent to Federal Standard 209 Class 100 or better, is often required. This classification ensures a maximum particle count of 3,520 particles per cubic meter of size 0.5m or larger.
Impact of Federal Standards on Cleanroom Design
Federal Standard 209 Class 100 or better necessitates a rigorous design approach. Our cleanrooms are engineered to facilitate a high level of control over particulate contamination, which is critical for sensitive biotech processes.
Necessity of Specific Classifications for Biotech Applications
Biotech applications often involve the manipulation of biological samples that are highly susceptible to contamination. Specific ISO classifications are necessary to create an environment that minimizes this risk, ensuring the safety and efficacy of biotechnological products.
Influence of Standards on Operational Protocols
Standards directly influence the operational protocols within cleanrooms. From the airflow patterns to the materials used in construction, every aspect of our cleanrooms is designed to meet these stringent requirements, ensuring that you can maintain the highest levels of cleanliness and control.
Design Considerations for Biotech Cleanrooms
When designing and constructing biotech cleanrooms, several architectural considerations are paramount to ensure a controlled environment that meets the stringent requirements of biotechnological processes.
Architectural Considerations for Cleanroom Construction
The architectural design of a cleanroom is critical for effective contamination control. At G-Con, we focus on creating layouts that facilitate unidirectional airflow, minimizing turbulence and potential contamination. The integration of pass-throughs for materials and equipment also helps to maintain the integrity of the clean environment.
Material Selection for Contamination Control
Choosing the right materials for surfaces, walls, floors, and ceilings is vital for preventing microbial growth and ensuring easy decontamination. Our cleanrooms utilize non-porous materials that are resistant to harsh cleaning agents, contributing to the longevity and cleanliness of the environment.
Optimization of Cleanroom Design for Biotech Processes
Cleanroom design can be optimized for biotech processes by customizing the layout to accommodate specific equipment and workflows. This ensures that critical processes are conducted in an environment that supports sterility and efficiency.
Benefits of Modular Construction
Modular construction, as provided by G-Con, offers flexibility and rapid integration. These prefabricated units can be quickly assembled and easily reconfigured to adapt to the evolving needs of the biotech industry, making them a beneficial choice for organizations looking to scale operations.
Air Filtration and Environmental Control Systems
In biotech cleanrooms, the air filtration and environmental control systems are engineered to maintain stringent cleanliness standards and create a stable, controlled environment conducive to sensitive biotechnological processes.
Contribution of HEPA and ULPA Filters
HEPA (High-Efficiency Particulate Air) and ULPA (Ultra-Low Particulate Air) filters are critical components in our cleanroom air filtration systems. They are designed to trap a significant amount of very small particles, with HEPA filters capturing at least 99.97% of particles 0.3 microns in diameter and ULPA filters capturing at least 99.999% of particles 0.12 microns or larger.
Role of Air Circulation in Contamination Prevention
Effective air circulation is essential for preventing contamination. Our cleanrooms utilize advanced airflow dynamics to ensure a consistent and unidirectional flow of filtered air, effectively removing contaminants and preventing stagnant air pockets where particulates could accumulate.
Control of Temperature, Humidity, and Atmospheric Pressure
Maintaining precise control over temperature, humidity, and atmospheric pressure is crucial for biotech cleanrooms. Our environmental control systems are optimized for specific biotech processes, ensuring that these parameters are kept within the narrow ranges required for your critical work.
Importance of Environmental Monitoring
Continuous environmental monitoring is vital for cleanroom integrity. At G-Con, we partner with entities like Sure BioChem Laboratories to provide precise monitoring solutions, ensuring that any deviations from the required conditions are quickly detected and addressed, safeguarding your operations and compliance.
Contamination Control and Cleanroom Protocols
Effective contamination control is the linchpin of biotech cleanroom operations. At G-Con, we emphasize the importance of stringent gowning procedures and decontamination practices to minimize human-induced contamination.
Essential Gowning Procedures for Cleanroom Personnel
Gowning procedures are a critical first line of defense against contamination. Our protocols require personnel to don cleanroom-approved apparel, including gowns, gloves, masks, and shoe covers, in a specific sequence to reduce particulate generation. This process is performed in designated gowning areas to prevent contaminants from entering the cleanroom.
Variations in Cleaning and Decontamination Practices
Cleaning and decontamination practices are tailored to the specific needs of each biotech cleanroom. We utilize a range of cleaning agents and biodecontamination processes, ensuring that all surfaces are free from particulates and microbial contamination. Regular cleaning schedules and the use of autoclaves for sterilization are part of our comprehensive approach.
Protocols for Minimizing Human-Induced Contamination
To ensure minimal human-induced contamination, we enforce strict behavioral protocols within the cleanroom. This includes controlled movements to reduce air turbulence and adherence to proper procedures when handling materials and equipment.
Importance of Personnel Training
Personnel training is fundamental to maintaining cleanroom standards. Our training programs cover gowning techniques, behavior within the cleanroom, and proper use of equipment, ensuring that all staff are proficient in the practices that uphold the integrity of your biotechnological processes.
Essential Equipment for Biotech Cleanroom Operations
In biotech cleanrooms, the selection of appropriate equipment is crucial for maintaining a contaminant-free environment and ensuring the precision of your research and production.
Core Equipment in Biotech Cleanrooms
Our cleanrooms are equipped with specialized furniture designed to meet the demands of biotech applications. This includes workstations that are easy to clean and maintain, as well as storage solutions that prevent contamination. We also provide advanced materials for cleanroom construction that offer superior performance in preventing contamination.
Enhancing Functionality Through Technology Integration
Integration of technology such as Building Management Systems (BMS) and Environmental Monitoring Systems (EMS) is pivotal. These systems allow for real-time monitoring and control of cleanroom conditions, ensuring that any deviations are promptly addressed.
Optimizing Cleanroom Efficiency with Strategic Equipment Layout
The layout of equipment is strategically planned to optimize workflow and maintain the integrity of the clean environment. We consider the specific processes and equipment you use to design a layout that enhances operational efficiency and minimizes the risk of contamination.
Importance of Equipment Validation and Calibration
Validation and calibration of equipment are non-negotiable in biotech research. Regular calibration ensures that equipment performs accurately, which is essential for the validity of your research outcomes. Our cleanrooms are designed to facilitate easy access for equipment maintenance and calibration, ensuring that your operations remain precise and reliable.
Monitoring, Validation, and Compliance in Biotech Cleanrooms
Ensuring compliance with regulatory standards is a cornerstone of our cleanroom solutions. At G-Con, we provide systems and protocols that support continuous monitoring, validation, and adherence to cGMP and 21CFR Part 11 requirements.
Continuous Monitoring in Biotech Cleanrooms
Continuous monitoring is implemented through state-of-the-art systems that track particulate levels, temperature, humidity, and pressure differentials. Our partnership with Sure BioChem Laboratories ensures that your cleanroom’s environmental conditions are constantly assessed for compliance with the necessary standards.
Validation Processes for Regulatory Compliance
Our validation processes are comprehensive, encompassing:
- Installation Qualification (IQ) to verify correct installation of equipment and systems.
- Operational Qualification (OQ) to demonstrate that systems operate according to specifications.
- Performance Qualification (PQ) to confirm that systems consistently perform as intended.
These processes are essential for meeting regulatory compliance and ensuring the safety and efficacy of your biotech products.
Meeting cGMP and 21CFR Part 11 Compliance
Our cleanrooms are designed to meet cGMP guidelines, which are critical for pharmaceutical manufacturing. We also ensure that electronic records and signatures comply with 21CFR Part 11 regulations, providing you with a cleanroom environment that upholds the highest standards of product quality and safety.
The Role of Documentation and Record-Keeping
Accurate documentation and record-keeping are vital components of cleanroom operations. Our systems facilitate meticulous record maintenance, ensuring traceability and accountability that are essential for regulatory inspections and audits.
Innovations in Cleanroom Technology
The biotech industry is continually evolving, and with it, the technologies that support cleanroom design and operation. At G-Con, we are at the forefront of integrating these advancements to enhance the functionality and efficiency of our cleanrooms.
Recent Technological Advancements
Recent innovations in cleanroom technology include:
- Smart Monitoring Systems: These systems provide real-time data on cleanroom conditions, allowing for immediate adjustments and enhanced compliance.
- Advanced Filtration Solutions: The use of nanotechnology in filtration systems has significantly improved the efficiency of contaminant removal.
- Prefabricated POD Cleanrooms: G-CON’s prefabricated POD cleanrooms offer rapid integration and flexibility, with the added benefit of being Factory Acceptance Tested.
Future Trends Impacting Cleanroom Standards
Looking ahead, we anticipate that:
- Digital Transformation: The integration of digital tools, such as smartPOD and automation systems, will streamline cleanroom operations.
- Sustainability: There is a growing emphasis on sustainable design, which includes energy-efficient HVAC systems and materials that reduce environmental impact.
Importance of Technological Advancements
Staying abreast of technological advancements is crucial for several reasons:
- Regulatory Compliance: Innovations can help ensure that cleanrooms meet evolving regulatory standards.
- Operational Efficiency: New technologies can optimize cleanroom operations, reducing costs and increasing productivity.
- Competitive Edge: Leveraging the latest cleanroom technologies can provide a competitive advantage in the fast-paced biotech industry.
By embracing these innovations, G-Con ensures that your cleanroom is equipped to meet the current and future demands of the biotech sector.
Challenges and Solutions in Biotech Cleanroom Management
Managing a biotech cleanroom involves navigating a range of challenges, from maintaining stringent contamination controls to adapting to rapid industry changes. At G-Con, we understand these complexities and offer solutions designed to address them effectively.
Common Challenges in Cleanroom Operations
Cleanroom technicians and managers often face challenges such as:
- Maintaining Environmental Stability: Consistently controlling particulate levels, temperature, and humidity.
- Regulatory Compliance: Keeping up with evolving standards and ensuring all processes are compliant.
- Operational Efficiency: Balancing the need for a sterile environment with the demands of productivity.
Modular Cleanroom Solutions by G-Con
Our modular cleanroom solutions provide:
- Flexibility: Easily reconfigured layouts to meet changing process requirements.
- Rapid Integration: Prefabricated components allow for quick assembly and scalability.
- Customization: Tailored designs to support specific biotech applications.
Implementing Continuous Improvement Practices
We advocate for continuous improvement practices through:
- Regular Monitoring: Utilizing advanced systems for real-time environmental tracking.
- Feedback Loops: Encouraging open communication channels for staff to suggest operational enhancements.
- Training Programs: Ongoing education for personnel on the latest cleanroom technologies and protocols.
The Importance of Adaptability
Adaptability is crucial in biotech cleanroom management due to:
- Technological Advancements: Keeping pace with new equipment and processes that can impact cleanroom design.
- Regulatory Changes: Ensuring compliance with the latest industry standards.
- Market Dynamics: Responding to shifts in biotech research and manufacturing demands.
By prioritizing adaptability, we ensure that your cleanroom remains a state-of-the-art facility, capable of supporting the dynamic nature of the biotech industry.
Regulatory Considerations and Global Standards
Navigating the complex landscape of international regulations is critical for biotech cleanroom operations. At G-Con, we ensure our cleanrooms are designed to meet the diverse regulatory requirements across different regions.
Impact of International Regulations on Biotech Cleanrooms
International regulations dictate the design, operation, and monitoring of cleanrooms. They ensure that biotech products are safe, effective, and of high quality. Compliance with these regulations is not just a legal requirement but also a commitment to excellence in biotech research and manufacturing.
North American vs. European Cleanroom Standards
There are key differences between North American and European cleanroom standards. For instance, the EU GMP guidelines are often more prescriptive, detailing the specific requirements for cleanroom operations, while the US guidelines tend to be more performance-based, focusing on the outcomes rather than the processes.
Ensuring Compliance with Global Biotech Regulations
To ensure compliance, cleanrooms must adhere to the standards set by bodies such as the International Organization for Standardization (ISO) and various national regulatory agencies. Our cleanrooms are designed to meet these standards, including ISO 14644-1 and the respective regional GMP requirements.
Importance of Understanding Regulatory Nuances
Understanding the nuances of these regulations is vital for operating on a global scale. It ensures that biotech products can move seamlessly across markets and that cleanroom operations are not hindered by non-compliance issues. Our expertise in regulatory compliance positions you to confidently navigate the global biotech landscape.
Cost Management and Budgeting for Biotech Cleanrooms
Effective financial planning is essential for the design, construction, and operation of biotech cleanrooms. At G-Con, we understand that cost considerations are paramount in your decision-making process.
Primary Cost Considerations in Cleanroom Design and Operation
When planning for a biotech cleanroom, you must consider:
- Construction Costs: These include materials, labor, and the technology required to meet the stringent standards of a biotech cleanroom.
- Operational Expenses: Ongoing costs such as utilities, maintenance, and staffing are critical for budgeting.
- Compliance and Validation: Ensuring that your cleanroom meets regulatory standards can incur additional costs for testing and certification.
Contribution of Energy-Efficient Designs to Cost Savings
Energy-efficient designs can significantly reduce operational costs. Our cleanrooms are engineered to optimize airflow and temperature control, which can lower energy consumption and result in long-term savings.
Budget-Friendly Solutions with G-Con’s Modular Cleanrooms
G-Con’s modular cleanrooms provide a cost-effective solution by:
- Reducing Construction Time: Prefabricated components allow for quicker assembly, which can cut down on labor costs.
- Minimizing Disruption: Modular cleanrooms can be installed with less impact on existing operations, preventing costly downtime.
- Scalability: The ability to expand or reconfigure as needed prevents the need for costly new construction.
Importance of Financial Planning
Financial planning is critical to ensure that your cleanroom remains operational and sustainable over time. By carefully considering all potential costs and seeking efficient solutions, you can maintain a cleanroom that supports your biotech endeavors without compromising financial stability.
Tailored Cleanroom Design and Consultation at G-Con
At G-Con, we specialize in designing cleanrooms that are meticulously tailored to meet the unique requirements of your biotech applications. Our team of experts is dedicated to providing solutions that align with your specific needs, ensuring that your cleanroom facilitates the integrity and success of your biotechnological processes.
Why G-Con’s Modular Cleanrooms Stand Out
Our modular cleanrooms are designed with flexibility and efficiency in mind, making them a preferred choice for the biotech industry. They offer:
- Rapid Integration: Quick assembly and minimal disruption to existing operations.
- Customizability: Adaptability to meet the evolving demands of biotech research and production.
- High-Quality Standards: Compliance with ISO Class 5/Federal Standard 209 Class 100 or better.
Connecting with G-Con for Your Cleanroom Solutions
To discuss your cleanroom needs and how we can assist you, please reach out to us:
- Phone: Contact us at 979-431-0700 for a direct consultation.
- Location: Our headquarters are based in Texas, USA, where we lead in providing prefabricated cleanroom solutions.
Choosing G-Con for Your Next Project
Selecting G-Con for your biotech cleanroom project ensures that you benefit from our industry-leading expertise, innovative design, and comprehensive support. We are committed to delivering solutions that not only meet but exceed your expectations, ensuring that your cleanroom is a testament to quality and precision in the biotech industry.